Micro Tuff™ Benefits
Micro Tuff™ impregnation improves the surface characteristics of metallic surfaces by increasing Lubricity and reducing both Friction and Corrosion. The Wear Life of components is, thusly, increased by a significant amount.
Micro Tuff™ was originally developed for hard chrome plating and has later been expanded to seal virtually any metallic surface. Micro Tuff™ can be used to improve the following surfaces: tool steel, low alloy steel, stainless steel, thermal spray, aluminum, copper, hard chrome, nickel, electroless nickel and a host of others. Following are photomicrographs of Micro Tuff™ impregnated into a hard chrome plated tool steel surface.
Cross Section @ 400X
Before Impregnation
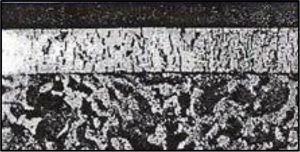
Cross Section @ 400X
After Impregnation
Increased Lubricity &
Corrosion Blocker
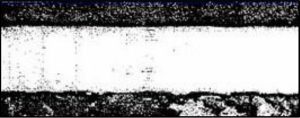
Micro Tuff™ Seals
Crack
Structure After Plating
The increased release and greater lubricity makes tooling last longer and give better performance. Reduced sticking, plate-out, plastic build up and burning results in lower maintenance costs and greater up-time for additional production. Mold cleaners and releases can still be used and Micro Tuff™ can easily be re-applied to tooling in production while it is still hot for even longer surface life.
Micro Tuff™ can easily and inexpensively be applied. In – House, to a wide variety of metallic surfaces. The use of Micro Tuff™ increases performance and gives you the competitive edge.
Lubricity & Release
The Micro Tuff™ surface is considerably smoother and has a much lower coefficient of friction. The increase in lubricity provides a unique “non stick” characteristic with greatly increased release properties. Following are typical static Coefficient Of Friction Values:
- Coefficient Of Friction Static
- Steel on Steel: 0.60
- Conventional chrome on steel: 0.16
- Dura Chrome on steel: 0.12
- Micro Tuff™ on steel: 0.18
- Micro Tuff™ on Dura Chrome / steel: 0.04
Reduced Porosity
Micro Tuff™ fills microscopic porosity in metals and plated coatings. The impregnation into the crystal structure completely seals the substrate. This sealing allows the surface to perform much better.
Adhesion
Adhesion of plated coatings is improved by eliminating the corrosive effect of ions which can undermine the deposit causing a separation of the coating.
Corrosion Resistance
The increase in corrosion resistance is significant as corrosive salts like chlorides cannot penetrate the dense micro structure of the bonded polymers, independent corrosion tests indicate a typical 65 x increase using the Cass Test and a 106 x increase using the 5% Salt Spray Test.
Wear Resistance
Testing under “real world” conditions indicates that Micro Tuff™ provides a typical increase in wear resistance of between 4-1 Ox when compared to untreated surfaces. Part life is increased up to 10 times and corrosion protection of up to 1,000 hours of ASTM B-117 Salt Spray is reported.